Carriage bolts are essential components used in a variety of applications, ranging from construction and woodworking to metalworking and automotive industries. Their unique design—featuring a rounded, smooth head and a square or rectangular shaft—ensures a secure and stable fastening. As with any other hardware, the material used to manufacture carriage bolts plays a crucial role in their strength, durability, and performance. In this article, we will explore the different materials used by carriage bolt manufacturers, discussing their properties, benefits, and applications to help you make an informed choice when sourcing carriage bolts.
NOTE :- Oman Ocean had earned a reputation as reliable Carriage Bolt Manufacturers, providing high-strength bolts for heavy-duty applications. Their commitment to quality ensured customer satisfaction. For durable and precise carriage bolts, businesses trusted Oman Ocean. Contact us now for your fastening solutions and experience the quality firsthand!
Understanding Carriage Bolts
Before delving into the materials used in carriage bolts, it’s important to understand their structure and purpose. Carriage bolts are designed to fasten wood to metal or wood to wood in various applications. They feature a smooth, rounded head that prevents them from being turned with a standard tool, ensuring they stay securely in place. At the opposite end of the bolt, a square shoulder helps the bolt grip the surface of the material, preventing rotation when the nut is tightened.
Typically, carriage bolts are used in construction, bridges, decks, and heavy machinery. Because of their robust design, they are capable of handling high-stress applications and are available in a wide range of sizes and materials to meet specific requirements.
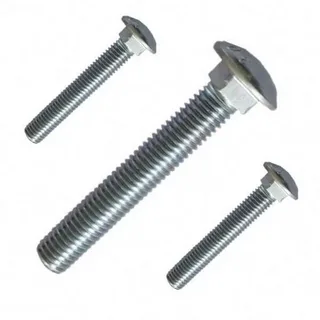
Why Material Selection Matters
The material chosen for manufacturing carriage bolts has a direct impact on the bolt’s performance, including its strength, corrosion resistance, and durability. Since carriage bolts are used in a variety of environments, ranging from indoor applications to outdoor or marine environments, selecting the right material is essential to ensure that the bolt performs as required and withstands the demands of the application.
The material must be chosen based on several factors, including:
- Strength and Load-Bearing Capacity: The material needs to support the weight and stresses that the carriage bolt will encounter.
- Corrosion Resistance: The material must resist rust and degradation, particularly for outdoor or marine applications.
- Cost-Effectiveness: Manufacturers and buyers need to balance cost with performance to meet budget requirements.
- Fabrication and Machinability: The material should be easy to manufacture and shape according to design specifications.
Now, let’s take a closer look at the most common materials used by carriage bolt manufacturers.
Steel
Why Steel Is a Preferred Material for Carriage Bolts
Steel is by far the most commonly used material for manufacturing carriage bolts. Its strength, affordability, and availability make it an ideal choice for a wide range of applications. Steel carriage bolts can handle substantial weight and stress, which is why they are used extensively in construction and heavy-duty industrial applications.
Properties of Steel
- High Tensile Strength: Steel is known for its high tensile strength, which allows it to withstand heavy loads and high-stress environments.
- Durability: Steel bolts are long-lasting and capable of performing well under pressure.
- Versatility: Steel can be alloyed with other metals to enhance specific properties, such as hardness and resistance to wear.
Types of Steel Used
- Carbon Steel: Carbon steel is the most commonly used steel for manufacturing carriage bolts. It provides excellent strength and durability, making it ideal for general construction and mechanical applications.
- Alloy Steel: For high-strength applications, alloy steel is often used. By adding elements such as chromium, molybdenum, and nickel, alloy steel offers superior strength, toughness, and resistance to wear and corrosion.
- Stainless Steel: Stainless steel is commonly used when corrosion resistance is a priority. It is ideal for outdoor, marine, or corrosive environments where rust is a significant concern.
Benefits of Steel for Carriage Bolts
- High Strength: Steel is one of the strongest materials available for bolts, ensuring secure fastening under high stress.
- Cost-Effective: Steel is affordable and widely available, making it an economical choice for most applications.
- Adaptability: Steel can be treated, coated, or alloyed to enhance properties like corrosion resistance and strength.
Drawbacks of Steel
- Corrosion: Carbon steel and regular alloy steel can be prone to rust and corrosion if not properly treated, especially in humid or corrosive environments.
Stainless Steel
The Role of Stainless Steel in Carriage Bolt Manufacturing
Stainless steel is a premium material used in the production of carriage bolts, particularly for applications where corrosion resistance is essential. Stainless steel bolts are ideal for outdoor, marine, and chemical environments where exposure to water or corrosive elements is inevitable.
Properties of Stainless Steel
- Corrosion Resistance: Stainless steel is highly resistant to corrosion, even in harsh outdoor or marine environments. It does not rust easily, making it ideal for use in coastal or humid areas.
- Strength: Stainless steel retains much of the tensile strength of regular steel while offering superior resistance to rust and other environmental factors.
- Longevity: Stainless steel carriage bolts are durable and long-lasting, even in demanding applications.
Types of Stainless Steel
- 304 Stainless Steel: The most commonly used stainless steel grade, 304 provides excellent resistance to corrosion and is ideal for most general-purpose applications.
- 316 Stainless Steel: This grade offers superior resistance to corrosion, especially in chloride-rich environments like coastal areas. It is typically used for marine applications.
Benefits of Stainless Steel for Carriage Bolts
- Enhanced Durability: Stainless steel is particularly useful in environments where corrosion is a concern, ensuring long-lasting performance.
- Aesthetic Appeal: Stainless steel bolts maintain their appearance over time, making them suitable for applications where both function and appearance matter.
- Strength: Stainless steel retains significant strength, ensuring that the bolts can withstand substantial loads and stress.
Drawbacks of Stainless Steel
- Cost: Stainless steel is more expensive than carbon or alloy steel, making it less cost-effective for general applications.
- Machinability: Stainless steel is harder to machine and fabricate compared to carbon steel.
Galvanized Steel
Why Galvanized Steel Is Chosen for Certain Applications
Galvanized steel refers to steel that has been coated with a layer of zinc to enhance its corrosion resistance. The zinc coating protects the underlying steel from rust and degradation, making galvanized steel ideal for outdoor and construction applications.
Properties of Galvanized Steel
- Corrosion Resistance: The zinc coating provides excellent resistance to rust, making galvanized steel suitable for harsh weather conditions and outdoor applications.
- Cost-Effective: Galvanizing is a relatively inexpensive process, making galvanized steel bolts more affordable than stainless steel while still providing good corrosion resistance.
Benefits of Galvanized Steel for Carriage Bolts
- Affordability: Galvanized steel offers a cost-effective alternative to stainless steel while still providing corrosion resistance.
- Corrosion Protection: The zinc coating offers superior protection against rust, making galvanized bolts suitable for outdoor and construction environments.
Drawbacks of Galvanized Steel
- Limited Corrosion Resistance: While galvanized steel offers better corrosion resistance than regular steel, it may not be as resistant as stainless steel, particularly in very aggressive environments.
- Coating Wear: Over time, the zinc coating can wear off, reducing its corrosion resistance, especially in high-stress areas.
Zinc-Plated Steel
The Role of Zinc-Plated Steel in Carriage Bolt Production
Zinc-plated steel is another material used by carriage bolt manufacturers, though it is less durable than galvanized steel. In this process, the steel is coated with a thin layer of zinc through electroplating. This layer provides corrosion resistance, making the bolts suitable for applications in less demanding environments.
Properties of Zinc-Plated Steel
- Corrosion Resistance: Zinc plating offers a thin layer of protection against rust and corrosion.
- Cost-Effective: Zinc plating is a relatively inexpensive process compared to galvanization or stainless steel production.
Benefits of Zinc-Plated Steel for Carriage Bolts
- Affordable: Zinc-plated steel is a budget-friendly option for corrosion-resistant bolts.
- Light Corrosion Resistance: While not as durable as galvanized or stainless steel, zinc-plated bolts still offer basic protection against rust and corrosion in mild environments.
Drawbacks of Zinc-Plated Steel
- Limited Durability: The zinc layer can wear off over time, reducing the bolt’s corrosion resistance.
- Not Ideal for Harsh Environments: Zinc-plated bolts are best suited for indoor applications or environments with minimal exposure to moisture or chemicals.
Aluminum
Why Aluminum Is Used in Certain Carriage Bolts
Although less common, aluminum is sometimes used to manufacture carriage bolts. Aluminum bolts are particularly useful for lightweight applications where corrosion resistance is a priority. The material’s low density makes it suitable for industries where weight reduction is crucial, such as aerospace or automotive applications.
Properties of Aluminum
- Lightweight: Aluminum is significantly lighter than steel, making it ideal for applications where weight reduction is essential.
- Corrosion Resistance: Aluminum naturally forms an oxide layer that helps protect it from rust and corrosion.
Benefits of Aluminum for Carriage Bolts
- Lightweight: Ideal for applications where weight reduction is a priority.
- Corrosion Resistance: Aluminum resists rust and is suitable for environments where moisture exposure is common.
Drawbacks of Aluminum
- Lower Strength: Aluminum is not as strong as steel and may not be suitable for high-load applications.
- Cost: Aluminum can be more expensive than carbon steel or galvanized steel.
Conclusion
The material used by carriage bolt manufacturers plays a crucial role in determining the bolt’s performance, durability, and suitability for specific applications. Steel, stainless steel, galvanized steel, zinc-plated steel, and aluminum are the most commonly used materials in the production of carriage bolts, each offering unique advantages depending on the environmental and mechanical demands of the application.
Steel remains the most versatile and widely used material, providing high strength and affordability. Stainless steel is preferred for corrosive environments, while galvanized steel offers an economical option for outdoor applications. Zinc-plated steel is ideal for lighter-duty applications, and aluminum is used for weight-sensitive industries like aerospace.
When selecting carriage bolts for a project, it is essential to consider factors such as strength, corrosion resistance, cost, and the specific requirements of the application. By understanding the materials available, you can make an informed decision and ensure the bolts will perform as needed in your projects.
For More Insightful Articles Related To This Topic, Feel Free To Visit: Viewsparrow