Selecting the right materials is essential for the strength, durability, and success of any construction or engineering project. One such crucial material is the PFC Channel (Parallel Flange Channel), a structural steel component used extensively in building frameworks, support structures, and fabrication works. Choosing the right PFC Channel involves more than picking the first available option. It demands a thorough understanding of the specifications, project requirements, and quality standards.
In this complete guide, we explore the seven essential rules for choosing the right PFC Channel to ensure optimal performance and longevity in your projects.
Understanding What a PFC Channel Is
Before diving into the selection process, it is important to understand what a PFC Channel is. A PFC Channel, also known as a parallel flange channel, is a U-shaped steel section with parallel top and bottom flanges. Unlike traditional tapered channels, the parallel flanges offer uniform strength distribution, making them ideal for a wide range of structural applications.
Common uses of PFC Channels include:
- Structural supports in buildings
- Frame construction for machinery and equipment
- Bridges and infrastructure projects
- Trailers and heavy vehicles
- Architectural and industrial frameworks
Their versatility and strength make PFC Channels a go-to choice for engineers and architects across industries.
Importance of Choosing the Right PFC Channel
Choosing the correct PFC Channel is vital to ensure the structural integrity, safety, and cost-efficiency of your project. A poor choice can lead to:
- Structural failures
- Increased maintenance costs
- Reduced lifespan of the structure
- Non-compliance with building codes
Following a systematic approach in choosing the right PFC Channel can eliminate these risks and result in a more successful project.
Rule One Understanding Load Requirements
The primary factor in selecting the right PFC Channel is understanding the load requirements of the structure. Different projects demand varying load-bearing capacities. Knowing the maximum load the channel needs to support helps in determining the appropriate size, thickness, and grade of steel required.
When assessing load requirements, consider:
- Static loads (permanent, non-changing weights)
- Dynamic loads (moving or fluctuating weights)
- Environmental loads (wind, seismic activity)
Consulting structural engineers and using precise load calculations ensures that the selected PFC Channel meets the safety standards for your specific application.
Rule Two Choosing the Right Size and Dimensions
- Height of the web (the vertical section)
- Width of the flange (the horizontal parts)
- Thickness of the flange and web
Different sizes offer different levels of strength, flexibility, and weight. Choosing the right dimensions based on project specifications guarantees that the channel will efficiently handle the applied forces without unnecessary material wastage or excessive costs.
Standard sizes are often listed in manufacturer catalogs, but custom sizing options are also available for specialized needs.
Rule Three Selecting the Appropriate Steel Grade
Not all PFC Channels are made from the same type of steel. Steel grades vary based on their mechanical properties, including tensile strength, yield strength, and corrosion resistance.
Common steel grades for PFC Channels include:
- S275: Suitable for general construction applications
- S355: Preferred for heavy-duty applications due to higher strength
- Galvanized options for enhanced corrosion resistance
Selecting the appropriate steel grade ensures the PFC Channel will perform optimally in the given environmental and load conditions. Higher-grade steels may have a higher upfront cost but offer better durability and lower maintenance over time.
Rule Four Considering Environmental Factors
Environmental exposure greatly influences the performance and lifespan of a PFC Channel. Factors to consider include:
- Humidity and moisture levels
- Exposure to chemicals or industrial pollutants
- Proximity to coastal or marine environments
- Temperature variations and UV exposure
In environments with high moisture or chemical exposure, galvanized or coated PFC Channels are recommended to prevent rust and corrosion. For extreme temperatures, selecting steel grades designed for thermal resilience is crucial.
Understanding the environmental demands of your project site ensures that the chosen PFC Channel will maintain structural integrity over the long term.
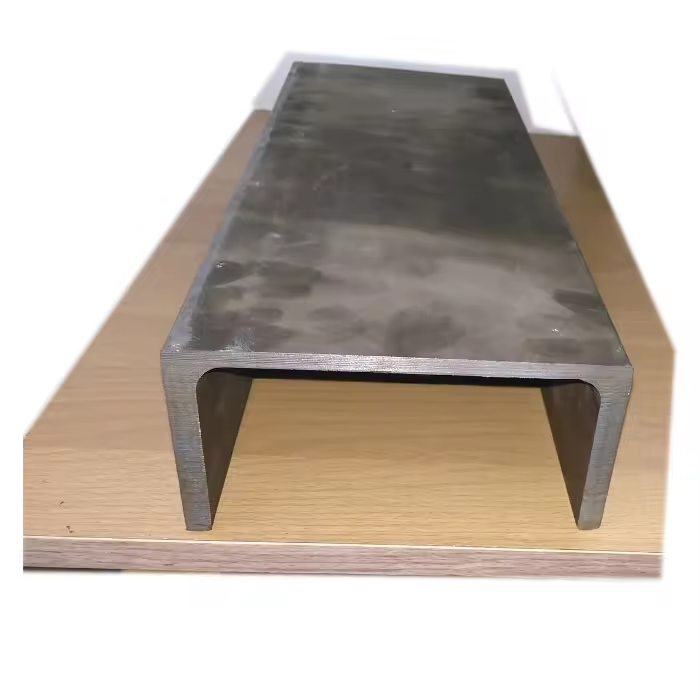
Rule Five Ensuring Compliance with Standards and Certifications
Compliance with national and international standards is non-negotiable when choosing a PFC Channel. Industry standards such as ASTM, BS EN, or AS/NZS specify the mechanical and chemical properties required for structural steel components.
Purchasing certified products guarantees:
- Consistency in quality
- Adherence to safety regulations
- Easier approval processes for building authorities
- Enhanced credibility of your project
Always request certification documents from your supplier to verify that the PFC Channels meet the necessary standards for your region and application.
Rule Six Evaluating Supplier Reputation and Capabilities
Choosing the right supplier is as important as selecting the right PFC Channel. A reputable supplier ensures product quality, consistent supply, technical support, and after-sales service.
When evaluating suppliers, consider:
- Industry experience and track record
- Range of products offered
- Ability to provide custom solutions
- Delivery timelines and logistics capabilities
- Customer reviews and testimonials
Working with an experienced and reliable supplier reduces project risks and ensures smooth execution.
Rule Seven Considering Cost Without Compromising Quality
While cost is an important factor in any project, choosing cheaper PFC Channels at the expense of quality can lead to higher long-term costs due to repairs, replacements, or even structural failures.
Focus on value over price. Invest in high-quality PFC Channels that offer durability, compliance, and performance, ultimately saving money by avoiding future expenses and downtime.
Request multiple quotes, compare specifications carefully, and look for a balance between cost, quality, and service to make an informed decision.
Common Applications Where PFC Channels Excel
Understanding where PFC Channels are typically used can also help guide your selection:
Building and Construction
PFC Channels are widely used for structural frames, lintels over doors and windows, and roof trusses. Their strength and ease of installation make them ideal for various construction needs.
Automotive and Transportation
The manufacturing of trailers, chassis frames, and transport equipment often utilizes PFC Channels due to their high load-bearing capacity and light weight.
Industrial Equipment
In heavy machinery, cranes, and manufacturing equipment, PFC Channels serve as critical components that ensure stability and structural strength.
Infrastructure Projects
Bridges, tunnels, and public works infrastructure often incorporate PFC Channels for support beams, retaining walls, and frameworks due to their resilience and reliability.
Benefits of Using PFC Channels in Modern Projects
The advantages of using PFC Channels are numerous and include:
- High strength-to-weight ratio
- Easy fabrication and installation
- Excellent load distribution
- Versatility across applications
- Cost-effectiveness compared to other structural options
- Recyclability and eco-friendliness
These benefits contribute to the growing popularity of PFC Channels in modern engineering and construction industries.
How to Maintain PFC Channels for Longevity
Proper maintenance practices can extend the lifespan of PFC Channels, ensuring they perform optimally for decades. Key maintenance tips include:
- Regular inspection for signs of rust, cracks, or damage
- Reapplication of protective coatings when necessary
- Prompt repair of minor damages to prevent escalation
- Keeping drainage paths clear to avoid water accumulation
- Periodic cleaning to remove debris and contaminants
Following a proactive maintenance schedule helps prevent costly repairs and preserves the structural integrity of the channels.
Conclusion
Selecting the right PFC Channel is a critical decision that impacts the success, safety, and cost-efficiency of any project. By following these seven essential rules — understanding load requirements, choosing the right size, selecting the appropriate steel grade, considering environmental factors, ensuring standards compliance, evaluating supplier reputation, and balancing cost with quality — you can make informed decisions that lead to successful project outcomes.
With careful planning and expert advice, the right PFC Channel will provide the strength, durability, and reliability needed for years to come.
For more insightful articles related to this topic, feel free to visit: viewsparrow
Leave a Reply